Ultrastrong and Lightweight Metal Structures Borrow Japanese Kirigami Technique
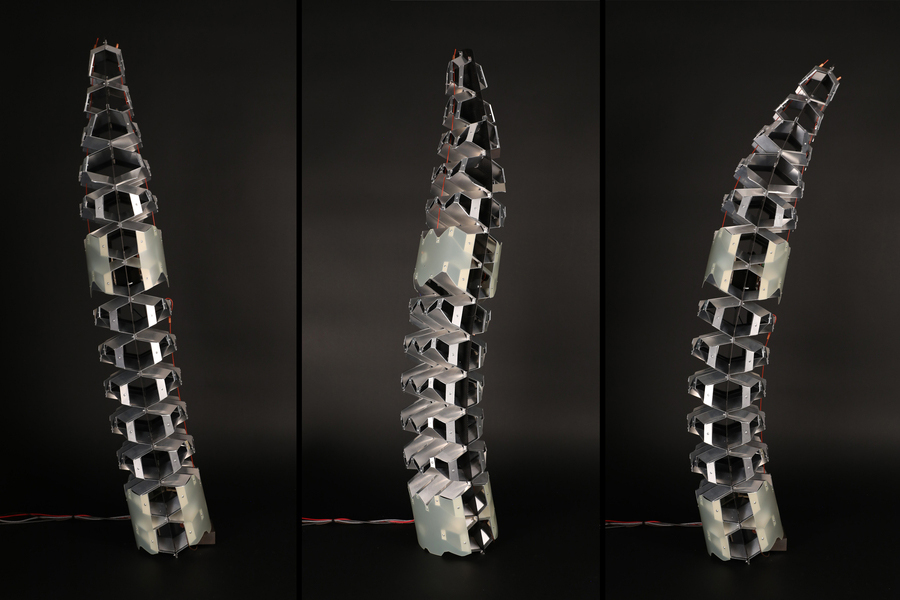
Modern engineering and design technology today demand better, stronger, cheaper, and lighter materials to form the core structures of many things. Traditionally, metal is the material of choice because of its strength and durability. But many factors affect the design and composition of these structures, such as weather, location, time, cost, and availability of materials. Transportation, for example, is one industry sector that requires these types of materials.
Architected materials inspired by nature
In nature, many living things have cellular solids comprising many cells packed together. Some of them look like honeycombs. The shape of these cells defines the mechanical properties of individual materials, including strength and stiffness. Bones, for example, is made up of a natural material that makes them lightweight yet strong and stiff.
Humans drew inspiration from cellular solids and bones to develop concepts for architected materials. Researchers changed the geometry of the unit cells of the natural materials to customize their acoustic, thermal, and mechanical properties. These architected materials have various applications, from heat-regulating radiators to shock-absorbing packing foam.
Architected material pivotal discovery from MIT
MIT researchers successfully manufactured a type of high-performance architected material called plate lattice. They borrowed the technique from an ancient Japanese art of paper folding and cutting – kirigami.
Using the technique, they can produce large-scale lattice plates to create structures from metal and other materials they can customize into required shapes with specific mechanical properties.
The senior author of the paper, Professor Neil Gershenfeld, who heads MIT’s Center for Bits and Atoms (CBA), explained that what they created resembles steel cork. However, it is lighter than cork but possesses higher stiffness and strength.
He further explained that they developed a modular construction process based on kirigami. They used several smaller components they formed, folded, and assembled into 3D structures. They produced ultrastrong and ultralight structures and robots that can morph and hold their shape depending on the specified load.
Despite being lightweight, these structures are stiff, strong, and easy to mass produce at bigger scales. They could be useful in producing aerospace, automotive, airplane, and architectural components.
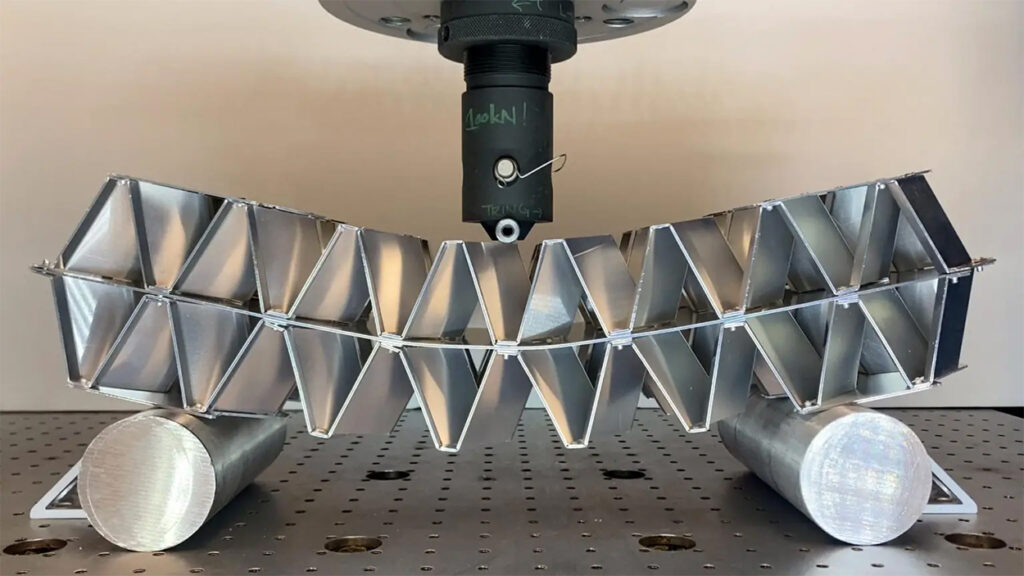
Fabrication through folding
Architected materials like lattices are usually used as cores for a sandwich structure, a composite material. Such truss lattices are lightweight but have high strength and stiffness.
On the other hand, plate lattices are cellular structures formed from the three-dimensional intersection of plates instead of beams. They are high-performance structures that are stiffer and stronger than truss lattices. However, they have a complex shape that challenges fabricators who use common techniques, including 3D printing, when required for large-scale engineering requirements.
In this regard, the MIT researchers surmounted the manufacturing challenges with the help of kirigami. Kirigami is already employed in producing plate lattices from partially folded zigzag creases. But for creating a sandwich structure, flat plates must be attached to the top and bottom of the corrugated core onto the narrow points created by the zigzag creases. Typically, this process requires welding techniques or strong adhesives. While effective, it slows down the plates’ assembly. Plus, the process is costly and challenging.
The MIT researchers modified the crease pattern using the Miura-ori pattern, which transformed the corrugated structure’s sharp points into facets with flat surfaces wherein they can attach the plates using rivets or bolts.
According to them, plate lattices perform better than beam lattices. With the breakthrough technique, they can now produce easier, faster, and cheaper plate lattices.
Customizing the patterns’ properties
With their innovative technique, they can customize the lattice plate’s mechanical properties, such as flexural modulus, strength, and stiffness. Since the structure is flexible and controlled, they could be used for robots and other dynamic applications where parts move, bend, and twist, such as spacecraft, cars, and airplanes.
However, the researchers realized that it was difficult to model their method. Therefore, they plan to develop CAD design tools for their kirigami plate lattice structures that are more user-friendly. They also want to explore new methods to reduce the computational costs of simulating such designs with specific properties.