MIT Sees Potential for Assembler Robots to Build Larger Structures
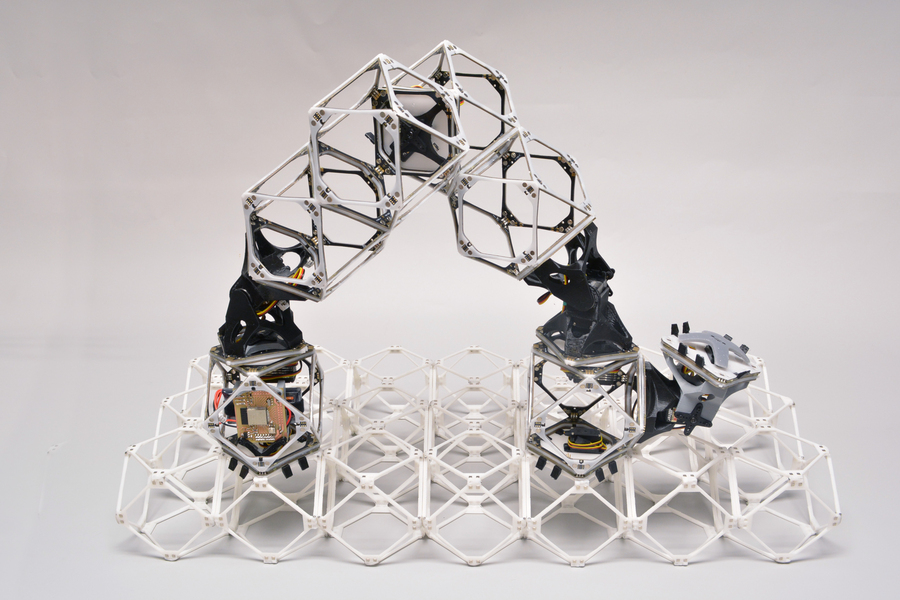
Many robots are purpose-built; thus, their sizes and shapes vary. Most robots perform individual tasks or work in conjunction with other robots.
MIT’s new work
The Center for Bits and Atoms (CBA), or MIT, has developed a new work based on their years of research in robotic technology. They also included their recent studies showing that they can use small identical lightweight items to help them assemble many functional objects. Moreover, robotic devices can help with the assembly work.
MIT researchers recently published their new work in the Nature Communications Engineering journal, citing that they can make the parts of a structure they are building and the assembler bots from similar subunits. At the same time, the robots move independently in big groups to complete large-scale structures faster. MIT has been doing considerable research in robotics for various applications.
The team leaders are Amira Abdel-Rahman, a CBA doctoral student, Neil Gershenfeld, CBA Director and professor, and three team members.
According to Prof. Gershenfeld, it is still years before a fully autonomous self-replicating robot assembly system becomes available. However, they are talking about a robot assembly system that can plan the best construction sequence and assemble larger structures such as larger robots.
However, MIT researchers are busy with the new work of making critical steps toward that goal. They are already working out the complex tasks of timing the building of more robots, deciding their size, and planning how to organize the groups of various sizes to create a structure efficiently and prevent the robots from crashing against one another.
Like their previous experiments, MIT’s new system necessitates large, usable structures they build from a range of small identical sub-units they call voxels (equivalent to a 2D pixel in volume). The team’s earlier voxels were structural pieces. The new voxels the team created are complex. Individually, each voxel can carry power and data from one unit to another, which enables the creation of structures that can carry out work and bear loads. They can manipulate, move, and lift materials as well as themselves.
The professor also explained that they must include intelligence when building structures. For example, several wires to their control system and a power source connected their assembler bots’ previous versions. From their experience, the team realized they needed structural electronics, meaning the voxels should be able to transmit force, power, and data. Thus, what their new system has are structures with no wires.
New assembler bots
In the new work of MIT researchers, the robots consisted of many voxels joined together. They can then take hold of another voxel with their attachment points on one end. The voxels move like inchworms to reach their target position, where the robots can attach and then release the voxel in the structure they are building.
In the MIT team’s earlier system, their assembler bots could build structures larger than the assembler bots’ size. However, they discovered that the process became inefficient because the assembled bots had to travel increasingly longer paths to bring each piece to the growing structure.
Autonomy
With their new system, the bots can decide autonomously if they need to make a larger version of themselves to reduce time in traveling longer distances. The larger robots can make even bigger robots during their construction process and can use the smallest robots to work on the finer details.
Another project leader, Amira Abdel-Rahman, said robotic devices face choices when assembling something. So part of their work for their new system is creating algorithms to help the robots make decisions. For example, the robots should learn where to start the path planning, divide the target shape into different areas and assign different robots. They already have the software that allows a person to input the shape and achieve an output defining where the bot should place the first block, etc.
Innovations and application
Prof. Gershenfeld said that thousands of papers were already published on robots doing route planning. But their team’s new system is unprecedented because their robots can build a different kind of robot or another one depending on the need.
However, their experimental system’s connectors are still not strong enough to carry the essential loads to conduct the assembly and carry the data and power links. Thus, the researchers are focusing on that. The robots can already walk and place parts, but they still have to achieve the bots’ capability to make a new robot that can walk away immediately. But they are already far enough into developing the system.
The researchers see several applications of the new system they developed. For example, building airplanes need huge factories that should be larger than the components they are building. So if the manufacturer is building a jumbo jet, they need to use another jumbo jet to carry the parts needed to build a new jumbo jet.
The small assembler robots can build the parts, and the only assembly process required will be the final assembly.
The team is working with NASA, aviation companies, and car companies. The researchers also see the new system’s application in the construction industry. For example, while 3D printing can build houses, it requires building larger printing machinery that is bigger than the house itself to create the parts. Thus, the MIT teams already see how the swarms of tiny bots will be beneficial to several industries. Also interested in MIT’s new work is the Defense Advanced Research Projects Agency. They are looking into the possibility of the assembler bots building strong structures for coastal protection against sea level rise and erosion. University of Houston associate professor of electrical and computer engineering Aaron Becker is not associated with MIT’s research. However, he considers the work an innovative hardware system that attacks the problem of reconfigurable systems-quickly assembling a robotic workforce to assemble the materials required for a defined structure efficiently. It is a radical approach to use a set of robot parts to build a new suite of robots in varying sizes to optimize the building of a structure quickly.