Green Chemistry Progress: NUS Method Achieves Significant Cost Reduction in CO2
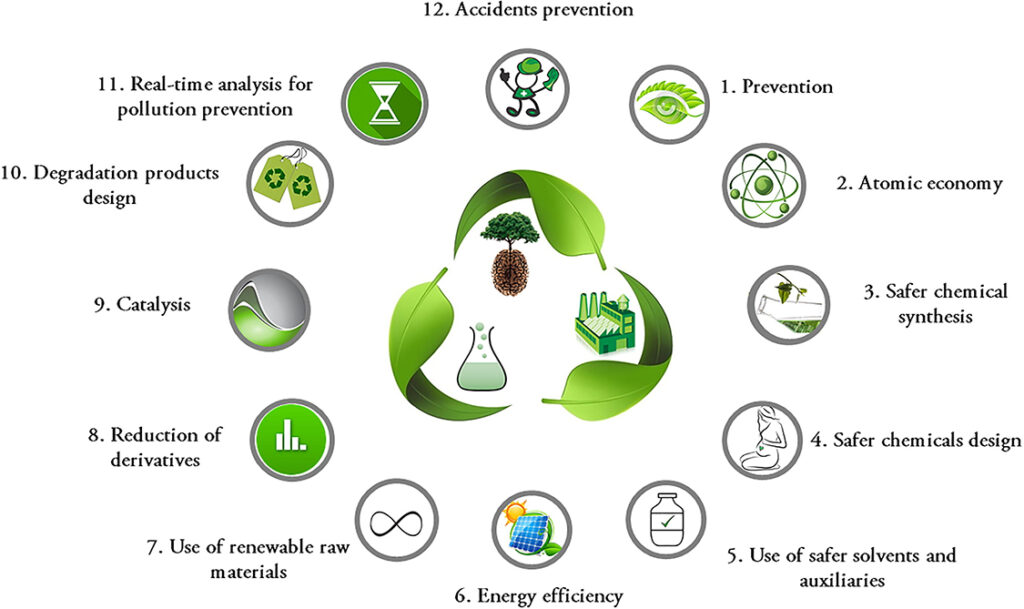
A Leap Towards Sustainable Chemical Manufacturing
NUS has just conceptualized a ground-breaking innovation in Green Chemistry that takes a giant step in the conversion of a key greenhouse gas — carbon dioxide — into useful chemical feedstock. This new process, spearheaded by Assistant Professor Lum Yanwei and his team from the Chemical and Biomolecular Engineering Department, Council, will in all possibilities provide the industry with a more sustainable and cost-efficient solution as compared to the present-day conventional techniques of chemical synthesis.
As the captured CO2 from treated flue gas is directly converted to desirable multi-carbon (C2+) products like ethylene and ethanol, the process, in reality, sets a new precedent to the industrial chemical manufacturing process, and at the same time, helps the cause of environmental preservation.
Innovation in Catalyst and Electrolyte Design
The core of the NUS team’s innovation lies in their unique integration of catalyst design with electrolyte selection, allowing for the direct conversion of CO2 from flue gases without the need for high-purity CO2. Traditional methods typically require the CO2 to be purified, a process that is both energy-intensive and costly. However, the new technique developed at NUS utilizes a specially designed nickel catalyst combined with a strategic selection of acidic electrolytes. This combination not only enhances the efficiency of the CO2 conversion process but also significantly reduces the presence of oxygen impurities which are known to cause undesired side reactions during the reduction process.
Economic and Environmental Impact
The benefits from the new process in terms of cost are significant, wherein we have a cost of around 30% lower CO2 conversion. Presently, the purification of CO2 has a cost of USD 70 to 100 per ton; this forms a significant part of the total cost of the processes. It will trim the cost of production yet at the same time reduce the energy footprint associated with manufacturing basic chemicals, which is contributed to by CO2 purification. This action represents a major step forward in reducing the ever-rising CO2 emissions that have led to climate change and can dramatically change the playing field for how industries will have to look at carbon capture and utilization.
Scaling Up and Future Applications
Aside from producing ethylene and ethanol, this process has a variety of other applications. By changing the catalyst system, this technique may produce acetate and propanol, both of which are required for adhesives and disinfectants. The versatility of this technology enables it to convert waste CO2 into a wide range of commercially useful chemicals. The NUS team is trying to increase energy efficiency and scalability in response to industry demand and ongoing conversations with potential partners. Their goal is to build prototype reactors for industrial application, which is a significant step toward integrated sustainability solutions in chemical manufacturing.
Assistant Professor Lum Yanwei and his colleagues at the National University of Singapore developed a sustainable and cost-effective method of converting waste carbon dioxide into valuable chemicals. This solution lowers operational costs by removing the need for high-purity CO2 and addresses the environmental issue of greenhouse gas emissions. The practice of effectively recycling a waste byproduct has the potential to alter chemical manufacturing and foster a more environmentally friendly future. The NUS method, which integrates science and sustainability, offers the potential to scale this technology for commercial applications while also contributing to economic and environmental goals.