GE’s ZEBRA Project Develops the Largest Recyclable Turbine Blade in the World
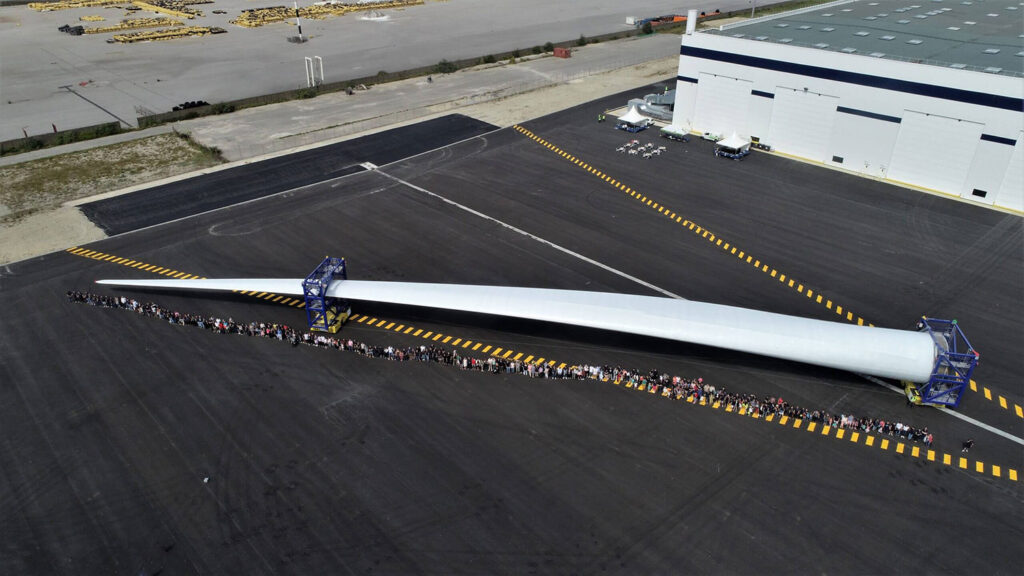
Fossil fuels provide energy and electricity to many industries and homes. They include natural gas, petroleum, and coal. However, the continuous use of fossil fuels releases large amounts of greenhouse gases, which destroy the environment and contribute to climate change.
According to projections, if the world continues to burn fossil fuels, it will deplete the entire supply by 2060. Thus, many experts in different fields combine their talents and skills to find and create alternative energy sources that will not harm our planet.
Wind turbines
Experts see wind turbines as alternative energy generator that does not use fossil fuels. Wind turbines do not create waste or produce matter that pollutes the environment. They are getting more popular today, but it has a long history.
The first wind turbine for electricity generation was built in Scotland in 1887. Prof James Blyth of Anderson’s College in Glasgow (Strathclyde University) constructed it. In the United States, the first known wind turbine to generate electricity was in Ohio. Charles Brush, an inventor, built it to provide electricity for his house.
Wind turbines have come a long way since then. However, although they are an efficient alternative, energy companies cannot recycle huge turbine blades.
General Electric’s solution
General Electric and the ZEBRA (Zero wastE Blade ReseArch) consortium found a way to develop a recyclable wind turbine blade. They already made a full-scale prototype of a 100 percent recyclable wind turbine blade made from thermoplastic. It is the largest recyclable thermoplastic blade in the world right now. It measured 62 meters and was designed and built by the LM Wind Power plant in Ponferrada, Spain. The company is a subsidiary of GE Renewable Energy.
LM Wind Power used the Elium resin manufactured by Arkema. The thermoplastic resin is renowned for its recyclable properties. Another critical component of the turbine blade is the high-performance glass fabrics from Owens Corning.
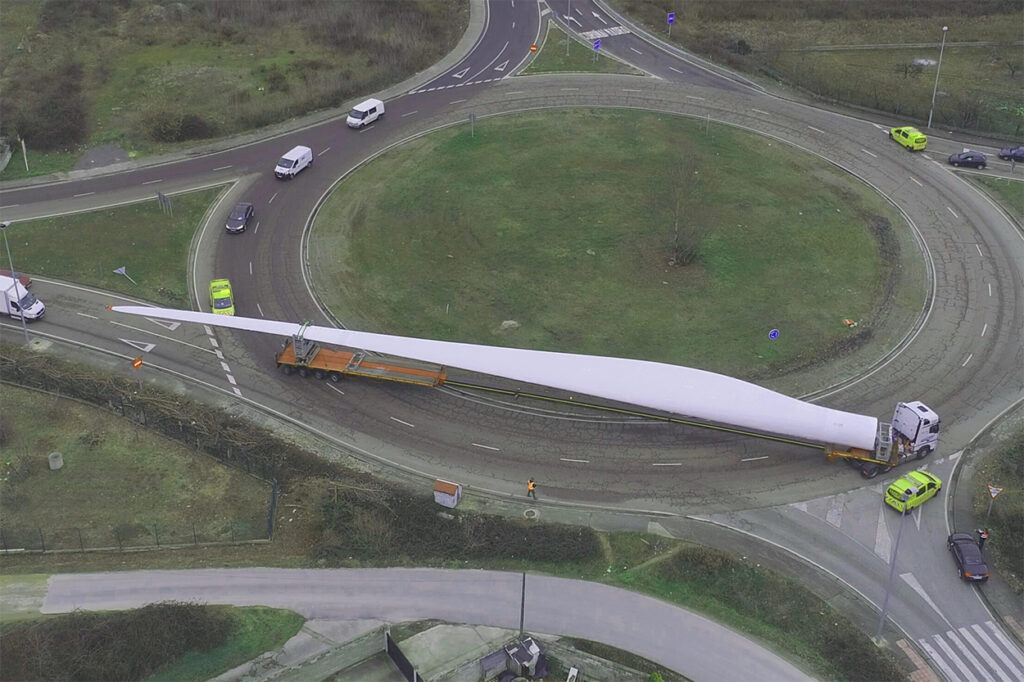
Testing the blade and its components
LM Wind Power has already started full-scale structural lifetime testing in Denmark’s Test and Validation Center. The company will verify the performance of the blade’s composite material and its usefulness in sustainable blade production in the future. After completing the tests, LM Wind Power will validate the end-of-life recycling methods and other means for production waste recycling.
Senior Director John Korsgaard of Engineering Excellence at LM Wind Power said they addressed two industry challenges through the project. First, they are fulfilling their Zero Waste Blades vision. They are preventing, as well as recycling wastes from the manufacturing process. Second, they are raising the level of blade recyclability. The thermoplastic composite blade is valuable. They can use recycling to produce other material compounds for different industries. It is also possible to depolymerize the blade and reuse the resin to create new blades.
GE’s ZEBRA Project started in September 2020. The consortium’s partners include IRT Jules Verne, a French research center, and several industrial companies. Other partners are SUEZ, Owens Corning, CANOE, LM Wind Power, Engie, and Arkema. Each partner will participate in the research and testing of the recycling, recovery, re-melting, and reusing of the blade’s components.
According to GE, the ZEBRA Project’s work schedule is going on as planned. It will end in 2023.The company expects the consortium to meet all the challenges of delivering the wind energy sector into the circular economy in a sustainable way.