Battery Bottlenecks: Tesla’s Cybertruck Struggles to Meet Demand
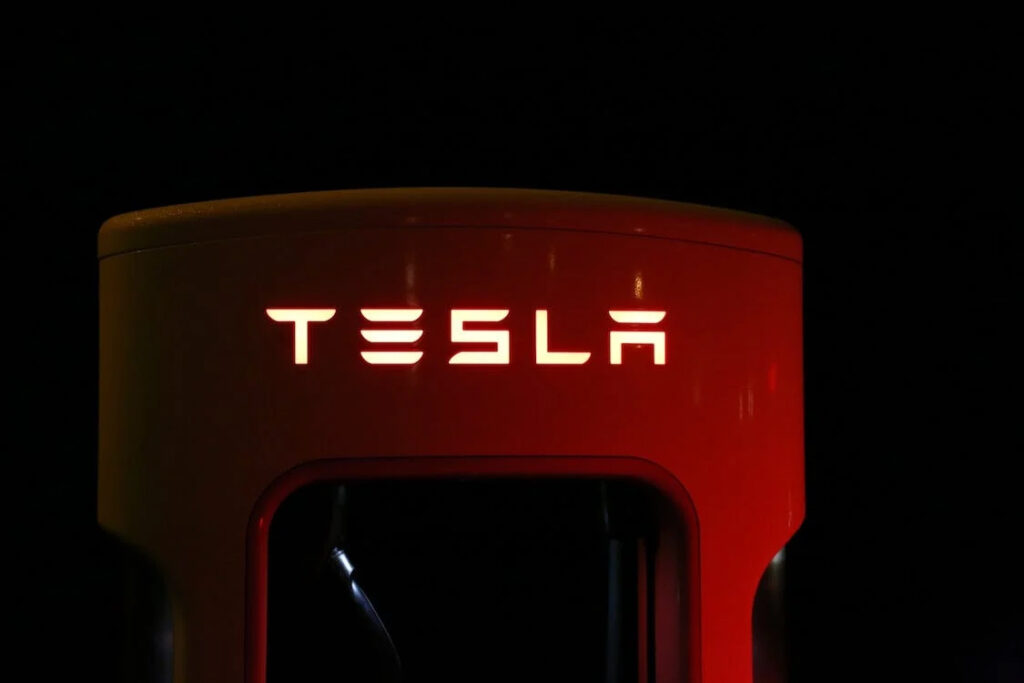
Tesla’s Cybertruck was a bold step into the future of electric cars, promising to combine cutting-edge technology, potent performance, and innovative design. From inception to customer driveways, the Cybertruck’s path highlights the immense obstacles and inventive spirit associated with creating next-generation battery technology within the intensely competitive automotive sector. This story examines the delicate dance between production and prototype, the advancements and difficulties in battery technology, and the wider implications for the industry as Tesla forges ahead on these uncharted territories.
The Cybertruck Vision: Prototyping vs. Production Realities
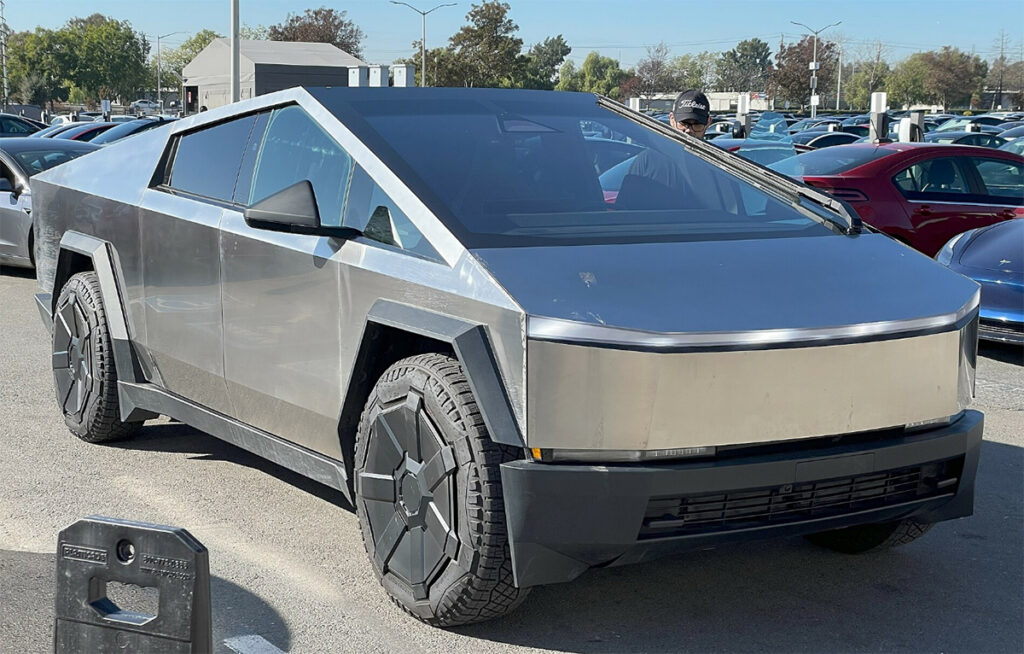
The Cybertruck, which reflects a future vision in contrast to vehicle manufacture, marks Tesla’s ambitious launch into the electric pickup market. It has proven difficult to transition from prototype to scale manufacturing of its 4680 battery cells. This stage, which Elon Musk refers to as “production hell,” exemplifies the ongoing battle in the automotive industry, where cutting-edge technologies and inventive designs frequently confront enormous challenges before they can be effectively and reliably manufactured for the general market.
Battery Breakthroughs and Bottlenecks: The 4680 Challenge
The 4680 batteries, a technological advance that promises increased energy density and lower prices, is at the center of the Cybertruck’s manufacturing challenge. This battery is essential to the Cybertruck’s success and the wider acceptance of electric vehicles. But producing these batteries to meet the rapidly increasing demand for Tesla vehicles has resulted in major bottlenecks, mainly because of the novel but untested dry-coating technology for electrodes, which, although theoretically superior, has proven hard to scale and perfect, a symbol of the larger industry challenge of striking a balance between innovation and the needs of high-volume, dependable, and reasonably priced manufacturing.
Scaling Up: Tesla’s Struggle with Dry-Coating Technology
Tesla’s specific struggle with scaling up production of the 4680 cells centers around the dry-coating technology. Implementing this more efficient process at an industrial scale has proven daunting, with significant challenges in consistently applying the technique to both anodes and cathodes, the latter presenting more complications due to its complexity and cost implications. The struggle to maintain quality and efficiency in this uncharted territory has led to production delays and is reflective of the broader tension in the EV industry between innovation and manufacturing practicalities.
Industry Implications: Competing in the EV Market Amidst Production Hurdles
The manufacturing constraints of the Cybertruck, particularly with the 4680 battery and dry-coating technology, have an impact on the EV sector. Competitors and the market are studying Tesla’s innovative initiatives, understanding the risks and benefits. These challenges impact customer expectations, market dynamics, and innovation, as other manufacturers learn from Tesla. Tesla’s actions may have an impact on industry standards, government responses, and electric car technology throughout the globe.
Tesla developed the Cybertruck to address battery technology and production capacity concerns, as well as to illustrate the potential and limitations of electric vehicle technology. The evolution of the Cybertruck from concept to mass-market demonstrates the significance of battery technology, environmentally responsible transportation, and the evolving automotive industry. As the industry learns from Tesla, the Cybertruck narrative will have tremendous impact on electric vehicle research, manufacture, and acceptance throughout the globe.