New, Stronger, and More Flexible Artificial Muscle for Robots and Haptic Technologies
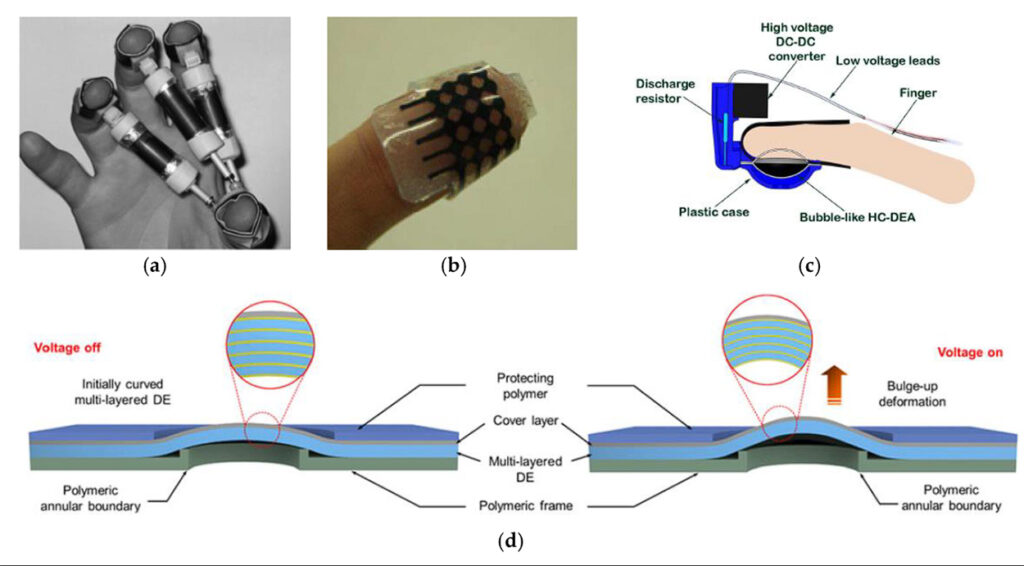
For several years, many scientists have tried to replicate human muscles to produce a muscle they can use for new haptic technologies and soft robots to improve their sense of touch. They have already succeeded in developing several soft materials that can remain viable under high-straining conditions and deliver a mechanical output.
New artificial muscles
Things are likely to change as the University of California, Los Angeles (UCLA) researchers recently announced their development of a new material to build stronger artificial muscles. According to their published research, the material is ten times more flexible than human muscles.
They call the class of materials they built dielectric elastomers (DE), which can deliver toughness and flexibility. In addition, the materials have high elastic energy density and are very light. According to scientists, it is possible to create DEs from synthetic or natural compounds. They are electroactive polymers that can change their shape and size with the application of an electric field. Therefore, the DEs are ideal for making actuators—machines capable of converting electric energy to mechanical functions.
A change in the manufacturing process
The dielectric elastomers manufactured today use silicone or acrylic, but while they are both functional, they have some disadvantages. The DEs that are made from acrylic can handle high levels of strain. However, they need pre-stretching and are less flexible. Silicone DEs, on the other hand, are easy to make, but they cannot deal with high strains.
The UCLA researchers, collaborating with SRI International, a non-profit organization, used commercially available chemicals and an ultraviolet light-based curing process to improve the condition of acrylic-based dielectric elastomer.
With the changes in the manufacturing process, the researchers managed to change the cross-linking in the polymer chains of the acrylic material, so the DE became flexible and softer. As a result, it became simpler to manipulate without the material losing form and strength or endurance even after repeated work cycles. Moreover, the changes they made in the manufacturing process allowed them to produce thin films. They called the new films PHDE or processable, high-performance dielectric elastomer.
Application of PHDE
The PHDE is an incredibly thin film, just as thin as human hair and lighter than a feather. Putting them in layers allowed the researchers to make small actuators that perform like muscle tissue and create enough mechanical energy to supply power to a tiny robot.
The layering of soft materials was already done in the past. However, the previous method researchers used employed a wet process where the liquid resin required depositing and curing. The results were not usually good, as the actuator had uneven layers. To prevent this from happening, the past artificial muscles they created only had one layer.
And this is where the UCLA PHDE film differs. While they still employed the layering process, they used a dry process. First, they laid the PHDE films in layers using a blade. Afterward, they cured the layers with UV light. Finally, the film layers were sandwiched between two electrodes to turn them into an actuator to change electrical energy into motion. The simplified method allowed them to manufacture actuators that appear like spider legs. The resulting actuators can bend and jump or windup and spin.
According to the research team, their new actuators can generate more force than biological muscles. They are also three to ten times more flexible than human muscles. In a demonstration, the actuator could toss a pea-sized ball 20 times its weight, according to a press release. Qibing Pei, a UCLA professor of materials science and engineering, said that this actuator could open the path for artificial muscles in new generations of robots and in wearable tech and sensors that can imitate or even surpass humanlike capabilities and motions. Professor Pei is one of the corresponding authors of the research, which was published in the journal Science.
The UCLA team believes their PHDE could produce soft robots with enhanced endurance and mobility. The same is true for new haptic and wearable technologies that need a keen sense of touch. In addition, their developed manufacturing process can help develop several soft thin-film materials for microfabrication, tissue engineering, and microfluidic technologies.