3D-Printed Soft Robotic Gripper Works Sans Electronics
Generally, robots make life easier for humans. They can continuously perform specialized and routine tasks with precision, unlike humans, who are prone to errors and need time to rest. Technological advancements and innovation produced different kinds of robots. One type that is seeing many applications is soft robots.
Soft robots provide safe human-machine interaction, simple gripping systems, adaptability to wearable devices, etc. Because of their unique features and advantages, soft robotics have wide applications, such as in origami muscle robots, prosthetic limbs, and wearable soft robots.
The potential of soft robotics
Soft robotics technology has plenty of potential for producing soft robots that can interact with humans and delicate objects. They are developed to prevent damage or harm to the things they touch or handle.
However, manufacturing such sturdy and soft devices is a challenge. The production process is time-consuming and complex because they must be pneumatically activated most of the time. Fabrication requires molding and assembling processes that need several manual operations, preventing developers from making complex designs. Moreover, even a simple robotic device would need complex control components.
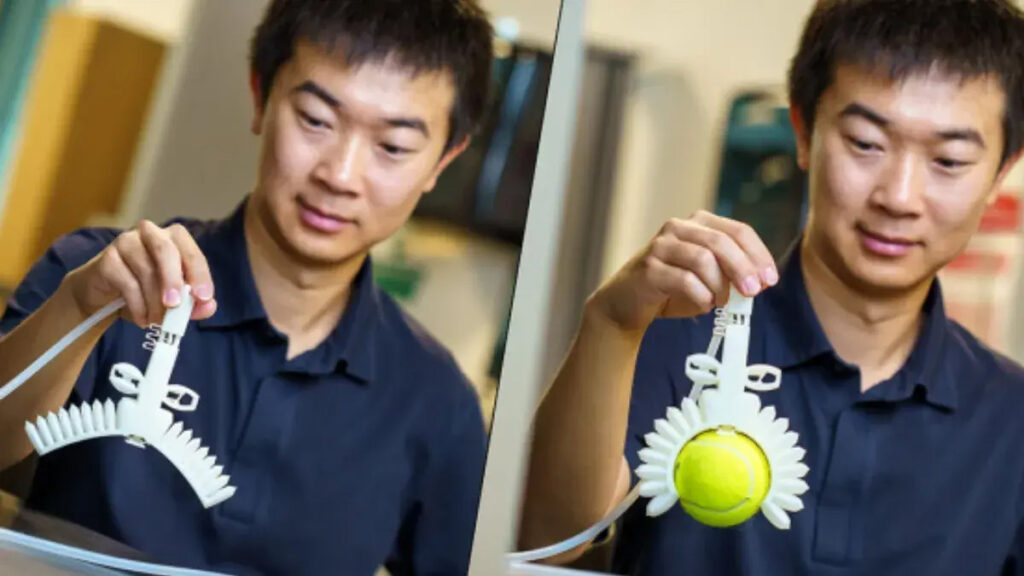
Non-electronic soft gripper
But things are likely to change soon. The University of California San Diego and BASF Corporation research team has produced a 3D-printed robotic gripper that can start working off the 3D printer. An outstanding feature of the soft robot is that it does not need electronics to make it work.
The research team said the soft gripper has built-in gravity and touch sensors that allow the device to pick up, hold, and release objects without using electricity or other means. The gripper releases the object once you turn it horizontally. The action activates a change in the airflow in its valves; thus, the gripper fingers relinquish their grip on the object it holds.
They could mount the gripper on the end of a traditional robotic arm if it is used for industrial manufacturing operations, fruit and vegetable handling, and food production.
With a new 3D printing method, the research team made the printer nozzle trace a continuous path through the individual layer’s entire pattern. Thus, the team avoided the introduction of any defects while printing. The new method likewise allowed the printing to be finer and more detailed in creating the structures. Furthermore, it minimizes the risk of defects and leaks in the printed item, a common issue when 3D printing softer materials.
The team’s new printing methods also allowed them to print thin walls up to 0.5 millimeters, which gave them a higher range of deformation and created a softer structure. The fabrication process requires no manual operation, such as part assembly and adjustment.
Although the soft gripper does not need electricity to make it work, it must be hooked up to a compressed air source. The gripper has channels and pneumatic valves that control a high-pressure flow of air that makes it function. An object in the gripper’s jaw activates the touch sensor, which allows compressed air to enter the internal channels to cause the device to hold the object securely. Correct rotation of the hand activates the gravity sensor to release the air pressure and cause the gripper jaws to open and release the object.
The research team sees a lot of potential for the gripper. It can be used for exploration tasks, research, farming, and manufacturing.